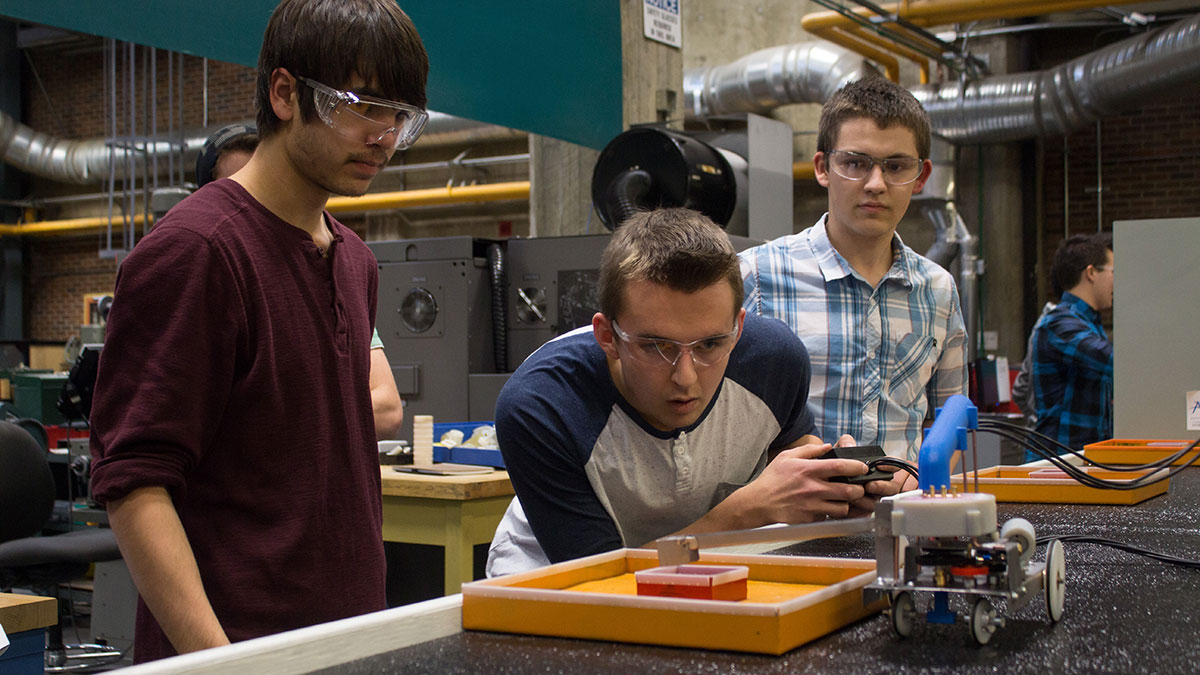
Over a hundred students packed into the Mechanical Engineering Lab on Monday, to watch and participate in a robot race.
As the practical component of their final project for Mechanical Engineering 260, the course’s 120 mechanical design students were broken into groups to create a motorized robot that would complete the “Just in Time” challenge.
“Just in Time” manufacturing refers to an inventory strategy where companies only receive goods as they are needed in the production process, thus reducing inventory cost, increasing efficiency and decreasing waste. The teams are first tasked with remotely delivering plastic spheres to specific boxes in a faux factory in the Mechanical Engineering Building, where the robots are then constructed. Points are then awarded for a device’s accuracy and speed.
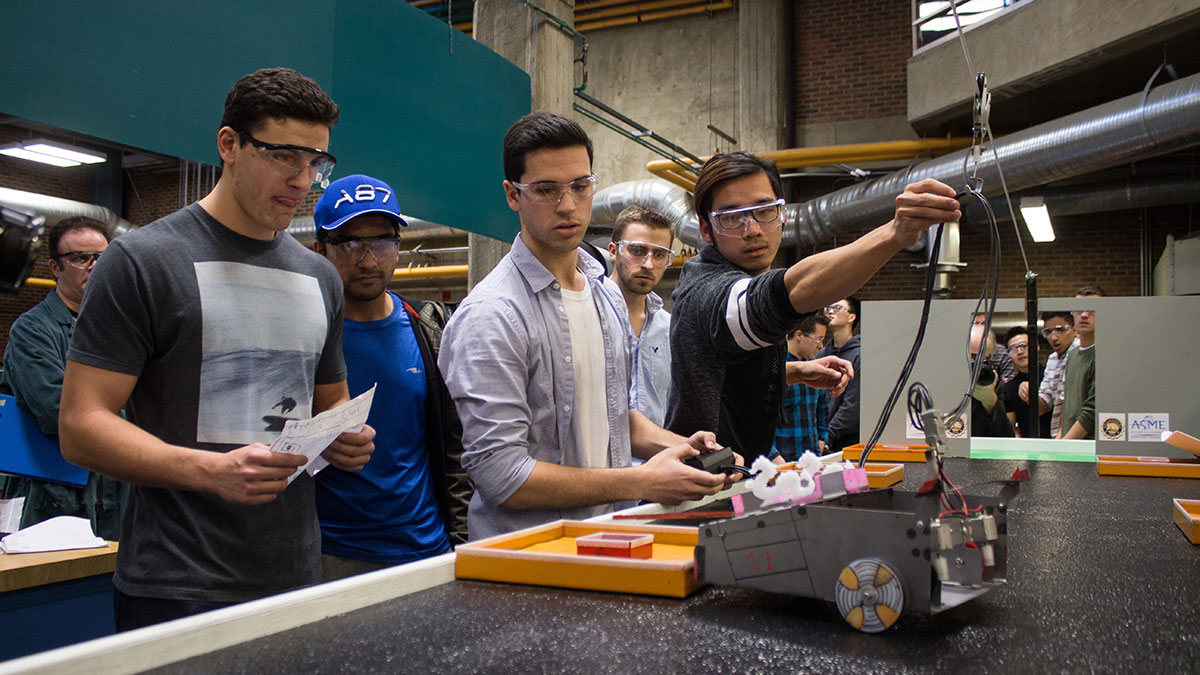
Andrew Campbell, a machinist technician at the Mechanical Engineering Lab, said a lot of time and effort goes into the creation of the contraptions.
“They really start building it three weeks ago,” Campbell said. “Everyone else is skiing over Reading Week and they’re here working hard and building. It’s the hardest five per cent (of their grade) they will ever work for.”
Aside from the workload, Campbell credits the project for helping students learn to work in a group environment. Throughout the design and build process, the students learn many of the skills they’d be expected to use in the work force upon graduation or during their co-op placement.
“This is what mechanical engineers do,” Campbell said. “They get problems and solve them using mechanics.”
One of the problems posed by this particular project was that the groups were only given two motors to carry out driving, steering, and sphere delivery functions. Team “Ricky Bobby,” comprised of students Noah Sherida, Jiefu Xia, Michael Primrose, Syndey Braaten and James Cho, came up with a unique design.
“We used one of the motors to drive the wheels, and attached the second to a system of gears so it would run the steering and delivery arm,” Xia said of their creation.
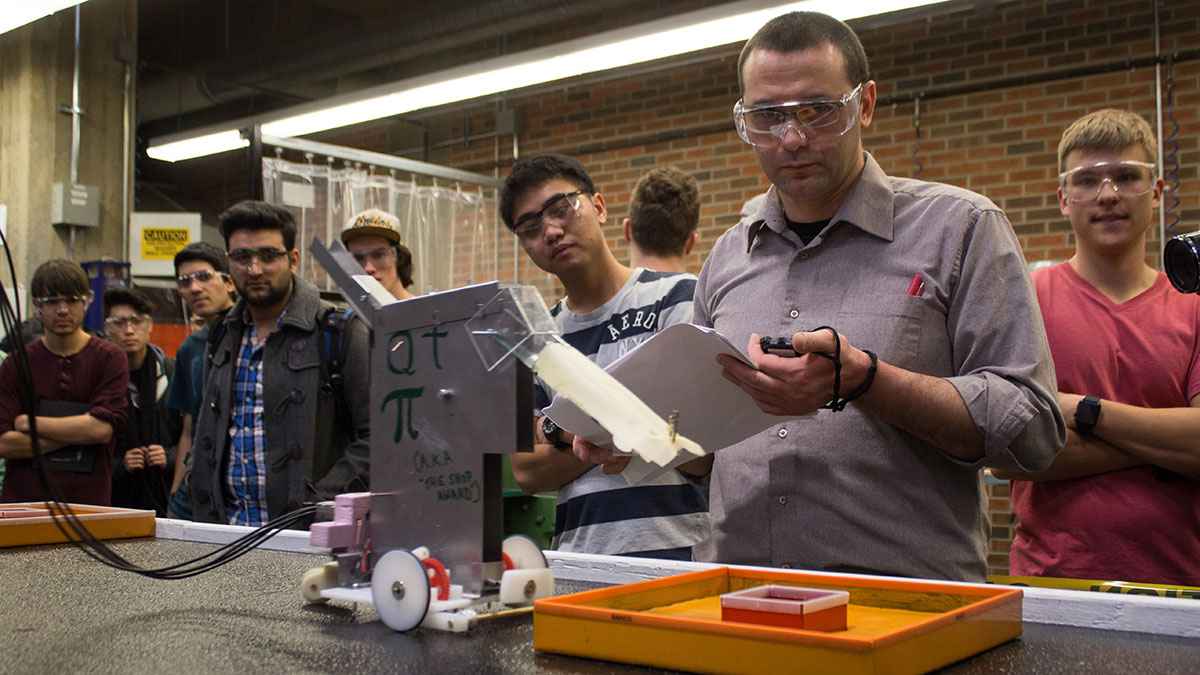
Sheridan credited his teammates with coming up with a solution to the two motor challenge. Primrose added that their method was more accurate and reliable than those who simply bumped into the box for sphere delivery.
“In real life, it’s more efficient to do it this way, to have two motors instead of three,” Sheridan said. “In an electrical vehicle application, it would use less power.”
After drawing names out of a hat, it was decided that Sheridan would pilot the vehicle for their timed run. Luckily, the test went well.
“We tried it this morning, and it took us exactly two minutes,” Sheridan said. “We just ran a one minute and 20 seconds at the test. I was pretty nervous, but it turned out OK.”
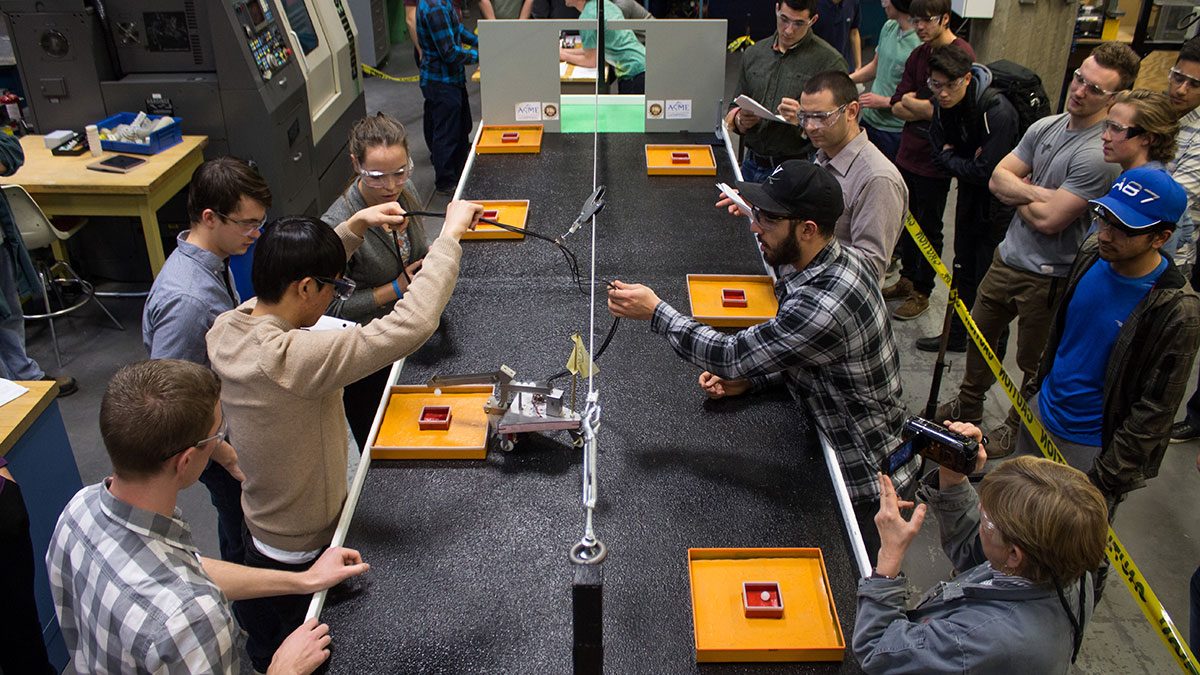
All of the group credited the hands-on approach encouraged by the course in making it a highlight of their semester. Xia pointed to the car project as a practical application of everything they learned in the classroom. This physical project led to Team Ricky Bobby spending almost 70 hours on their vehicle, but Braaten said it was all worth it in the end.
“It’s the most fun we have in a course,” Braaten said. “Even though it’s ended up being more time consuming than we thought.”
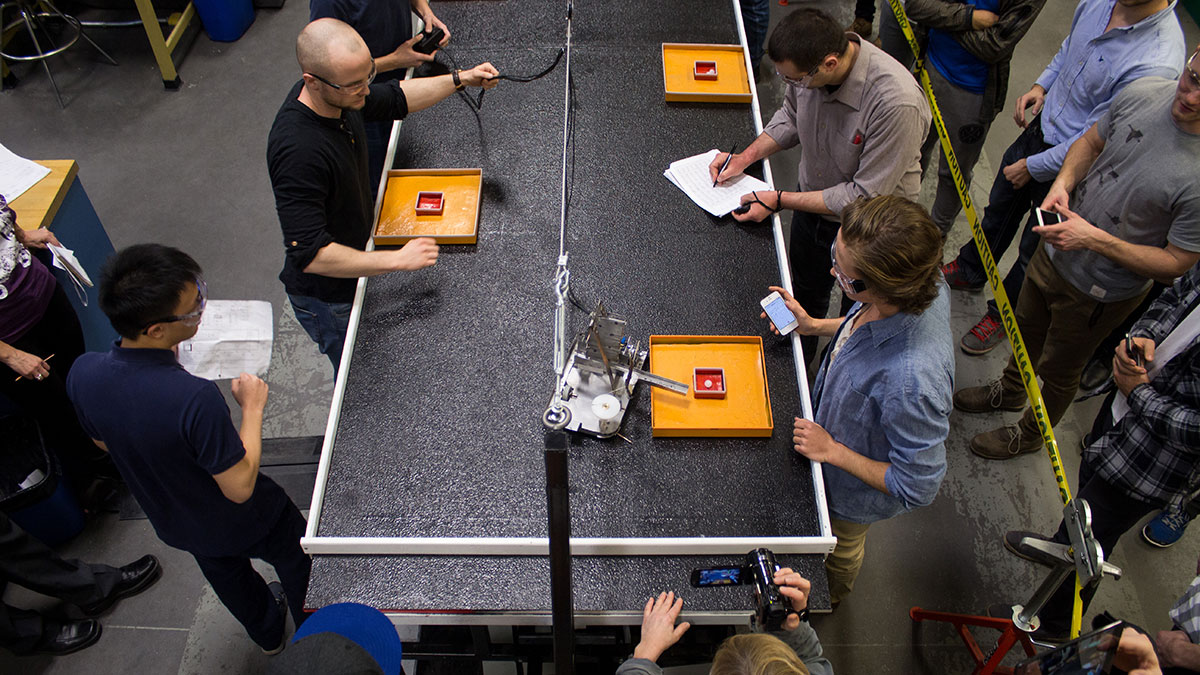